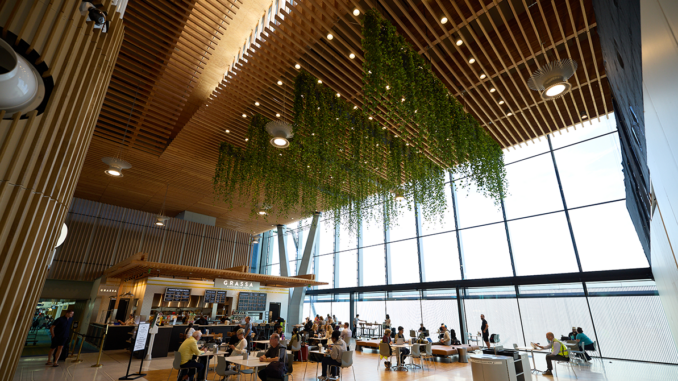
By / Jessica Kirby • Photos courtesy of McKinstry and Deamor
When the new main terminal is complete, the Portland International Airport (PDX) will be 175,000 square feet larger, but it will use half of the energy per square foot than it used to. Over its seven-year timeline, this project has achieved impressive new feats in many areas, including design, engineering, construction, energy efficiency, and, of course, sheet metal.
The main PDX terminal expansion, designed by ZGF Architects, has a $1.5 billion price tag and impresses with a design focused on health, wellbeing, and safety. Abundant aspects of nature, from a forest of live trees to a nine-acre mass timber roof, are spread throughout the building.
The terminal has flexibility built in with 100 ft x 150 ft long-span structures and unobstructed floorplates, which allow the airport the ability to successfully adjust to changing and future needs, creating column-free security checkpoints and adaptable check-in islands.
Its crowning achievement, figuratively and literally, is the nine-acre glulam roof that is set in an undulating pattern to maximize air flow and light, while achieving an unparalleled aesthetic. The 18-million-pound, 400,000-square-foot structure is held up by massive Y-columns fabricated from 1-inch plate steel and filled with thermal grout for fireproofing.
When walking through the terminal, the most striking feature of the roof is the dappled light filtering through the wood ceiling and the trees, invoking the feeling of walking through a Pacific Northwest forest.
SMACNA Oregon & Southwest Washington Represents
Several SMACNA Oregon & Southwest Washington and SMACNA-affiliated contractors contributed to this landmark project, Portland’s largest in history. Arctic was brought on to the project in 2019 under a design assist agreement. “For the first three years of the project, we worked with the design team to assist in finding a constructable design for the airport that balanced the architect’s vision with the need to provide a robust HVAC system that would make the environment comfortable for passengers and airport personnel,” says Aaron Vanrheen, COO at Arctic.
Arctic
The company was also responsible for finding temporary HVAC strategies to help keep the active parts of the airport heated and cooled during construction. By the time the TCore buildout started, Arctic had installed four new air handlers and several temporary systems to make the project ready for the new build.
“Our scope in the main build was to furnish and install the duct and airside equipment on the project,” Vanrheen says. “This included assisting in the installation of 34 air handlers, 24 CRAC/CRAH units, 44 fans, 160 terminal units, and more than 1,000 diffusers.”
By the end of the project, Arctic will have fabricated and installed over 700,000 lbs of duct, including Type 1 and Type 2 exhaust shafts (grease and dishwasher exhaust, respectively) for 22 future tenants.
As one would expect from a project of this magnitude, it wasn’t without its challenges. The project includes a large and expansive new structure that is tied to the existing structure, creating the potential to cause varied movement during structural settling or during a seismic event, since the new structure is built to very different standards than the existing structure.
“This created unique challenges in finding routing between the two structures that allowed for movement without compromising the HVAC system,” Vanrheen says. “Many of the challenges were solved during design by limiting how many duct systems crossed these boundaries between new and old, but in the areas where these boundaries needed to be crossed, Arctic helped address the issue by adding duct flex connectors to allow for some movement.”
McKinstry
James Slater, director architectural metals – Pacific NW Region for McKinstry, says the company’s scope was exterior cladding and interior decorative metal scopes, totaling over $30 million in value.
Over its time on the project, McKinstry hung 11,000 sf of exterior sunshades at the roof line with a crane and installed 72,000 sf of roll-formed cladding panels, 35,000 sf of aluminum composite cladding panels, 29,000 sf of interior sunshade/dec grille, and 13,000 sf of interior aluminum/stainless cladding panels. It was also responsible for exterior and interior louvers; roof flashings, skirt panels, and trims; interior components, such as column covers, guardrails, handrails, cane rails, and baggage handling panels; and miscellaneous trims, planters, and tree grate surrounds.
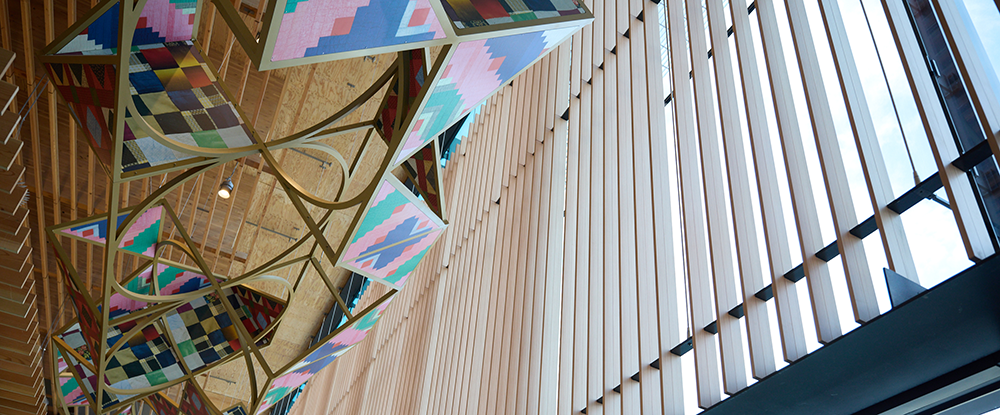
“The roof being prefabricated in football field size sections that were transported to the final site was a unique aspect of this project and took a lot of coordination,” Slater says. “We had a lot of early roof flashing and trim work that was done in the prefab stage.”
“We partnered with Just Right Heating and Cooling who has done some of the flashing fabrication and helped to coordinate the ordering and installation of the large sunshade scopes,” he says. “They were a great partner and did a great job.”
The airport had to remain fully operational during construction, and this required a great deal of logistical planning from general contractor Hoffman/Skanska and the Port.
“The Port required subcontractor teams be in lockstep with them,” Slater says. “This meant difficult access to certain areas and dealing with very high levels of security protocols.”
DeaMor
DeaMor skylights have provided natural daylight for the Port of Portland’s airport since 1988, starting with concourse K (now the westernmost segment of D) and the rest of concourse D, concourse C, and the south node over security at the intersection of concourses B and C.
“Having worked with ZGF and both Hoffman and Skanska on these projects, we were uniquely prepared to work with their joint-venture team,” says Jody Moore, a founding partner and president of DeaMor Skylights, who leads the design and preconstruction. “But none of the prior projects had the level of complexity or required the ingenuity and force of sheer will and confidence that PDX TCore required.”
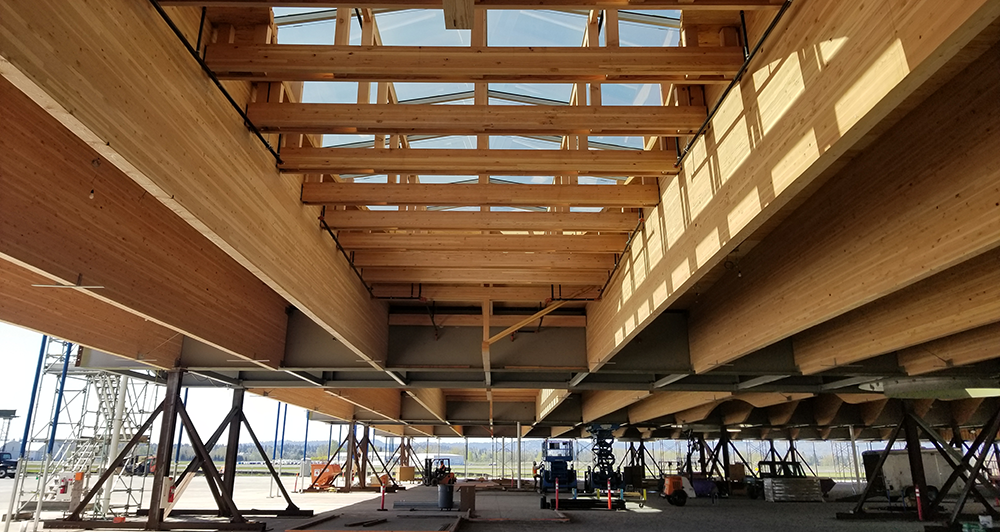
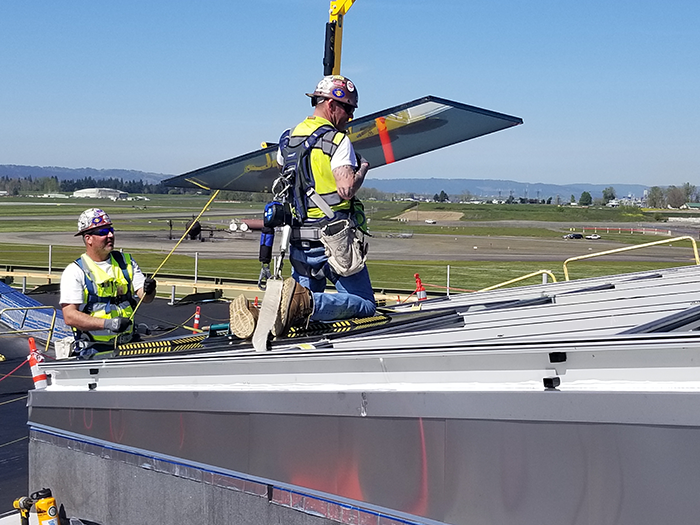
The project required 32,000 sf of glass to create 49 skylights in five different sizes. The framing is a structurally glazed, thermally broken tubular system with rafters and structural attachment clips designed and extruded specifically to meet the requirements for the roof. The aluminum is finished with an AAMA 2605 light silver fluoropolymer coating and each opening is finished with a custom stainless-steel coping provided by Local 16’s General Sheet Metal.
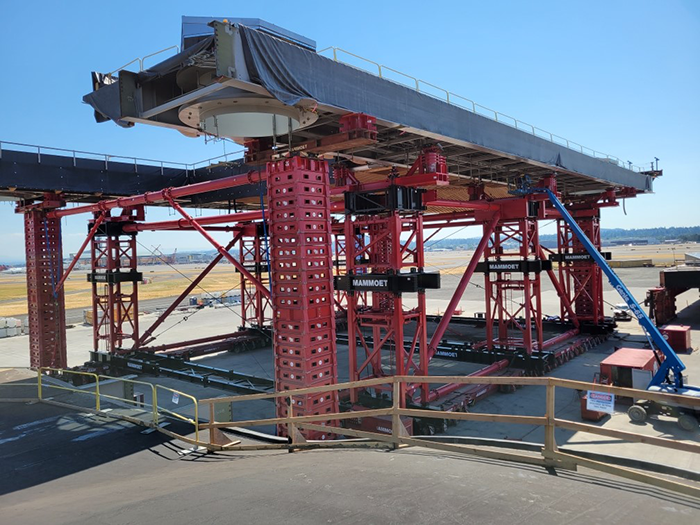
The skylights were shipped to the site knocked down and assembled on the roof, and the glass was hoisted to the openings. Installation took place on the 2.5-acre assembly slab located west of the airport, where complete roof modules were prefabricated with mechanical, electrical, roofing, and skylights fully installed. The height of the roof was 25-feet during installation, then raised to 75-feet and conveyed into place over the top of the existing terminal.
“The skylight system is engineered to provide opening protection without the use of screens or guardrails, specifically to accommodate access for workers during installation, maintenance, and future replacements,” Moore says.
Just Right Heating & Cooling
Just Right Heating & Cooling partnered with Arctic to complete HVAC ductwork and with McKistry to fabricate architectural panels, and install architectural blinds on the south and west walls of the building—all of which amounted to nearly a half a million pounds of fabricated metal.
“Most of the architectural panels for the skylights aren’t square, straight, or level, which meant each one had to be detailed, laser cut, packaged, and delivered,” says Just Right Heating & Cooling President, Daniel Miranda. “And there are thousands of them.”
The blinds were the first of their kind in the Portland area, supplied by a European company and manufactured in Texas. The mass timber parts were difficult to hang because the wood is breathing and changing with the temperature, which means the arch heights change throughout the day. To ensure the screens hang at the correct level, the roof is preloaded with weights. The screen system also includes aluminum bars on the south and west sides that are painted to look like wood.
“We are a small company that has been in the market 12 years and the only one on the project that was ‘homegrown’ from Local 16,” Miranda says. “We employ 63 workers from Local 16, and thanks to the Portland Airport and bigger companies like JH Kelly, McKinstry, and Arctic having trust in us, we have been able to grow the company.”
Other SMACNA Oregon & SW Washington members contributing to this project include Harder, who did plumbing, piping, and electrical, and JH Kelly who did piping and critical infrastructure work.
The project comprises four transformative projects including the expansion of Concourse E (completed in 2020), a new Concourse B (designed by ZGF and completed in 2021), a new Parking Addition and Consolidated Rental Car facility (completed 2021), and the main terminal expansion, scheduled for completion by 2025, with Phase 1 opening in August 2024.
The second phase opening is expected to be done in December 2025 or early 2026 and will feature nearly a dozen new local restaurants and shops, more restrooms, exit lanes to head to baggage claim and two new areas to wait for arrivals. ■