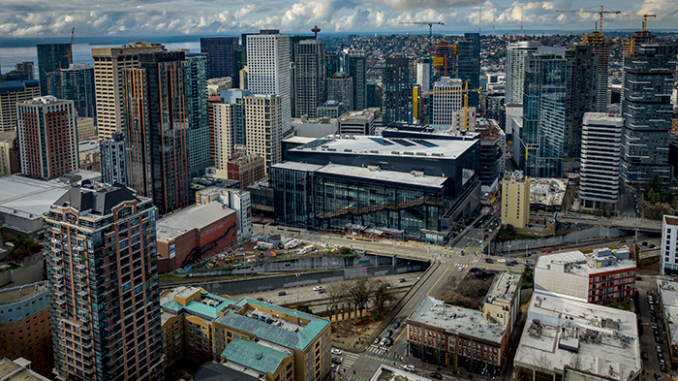
MacDonald-Miller completes its largest and most complex single-building project
By: Nicole Martin
The Summit building at the Seattle Convention Center, the largest single building MacDonald-Miller Facility Solutions has ever worked on, is now open. With a contract value over $100 million and several years of preconstruction work, the Conference Center addition had MacDonald-Miller starting onsite work in September 2019, setting the first four of 35 air handling units. After more than three years of construction, the building opened to the public on January 25, 2023.
Construction
MacDonald-Miller was selected for this complex project based on its project team experience and prefabrication expertise. That experience allowed the team to take an integrated approach to the design and building information modeling of the project. MacDonald-Miller was involved in pre-construction efforts starting in 2016, when the scope included providing and installing all the HVAC systems, including mechanical piping, sheet metal, and controls. The size and scope of these systems is incredible, with many duct sections bigger than a full-size train car. The project includes more than 1.6 million pounds of ductwork, with many long runs to accommodate the exhibition halls and gathering spaces. Some of the ductwork is more than 20 feet wide. The most unique aspects of this project included prefabricating a 4,000-ton central plant, creating complex life safety systems, and using a unique construction method due to the large building footprint, which required the steel structure to be installed in phases and presented several sequencing challenges.
Teamwork
Due to the sheer size, the project was a challenge from the start. “With 1.5 million square feet of single rooms spanning multiple city blocks, the construction sequence and logistics of this project are like nothing else in the country,” said Ryan Hunter, project manager at MacDonald-Miller.
“Adding the hurdles of the pandemic hitting during our peak crew size, a concrete strike, and challenging labor and procurement markets, the level of difficulty only increased. These challenges were met head-on by the project team, and we executed solutions to those challenges with distinction.”
Logistics
Most construction projects start on the ground and move up, so one of the biggest challenges of this site was that it was built in a billboard sequence. This unique plan organized the construction into five towers or “billboards” lined up in a row to brace one another and support the load. Area one went up first, then area two, and so forth, until all 14 levels were completed.
Another aspect unique to the project was that the scaffolding was not as permanent as it may have been on other sites. It sat in place for a day or two to load materials and then moved to a different location for walls to proceed.
During preconstruction, detailers from MacDonald-Miller co-located at the Arup Engineering office to model the systems in 3D to speed up the design and coordination process.
Collaboration was vital with engineers, detailers, and project managers all together in a room to resolve constructability issues early, which allowed MacDonald-Miller to prevent problems that would have been very costly to fix later. “Problems could have become serious later in the game had we not talked about them,” said Principal in Charge, Reagan Perry. “For instance, the early design had single coil air handlers that would have required very large headers. Our detailers saw that we could reduce costs and field piping by using dual coil air handlers and maximizing prefabricated headers.”
Rigorous constructability reviews allowed MacDonald-Miller to manage adjustments before the air handling units had been procured or installed.
The detailing department paved the way for success, creating thousands of work package deliverables. Due to the size of the floor plate, each level had to be broken into 15 separate drawings and included about 250 separate install drawings per trade.
“Our fabrication, logistics, and field teams performed phenomenally for this project,” said operations manager Rylan MacCay. “Ensuring the fabrication was accurate and that it arrived on site when the crews needed it was an enormous undertaking. Our team made over 2,800 deliveries to the site with fabrication, equipment, and other materials.”
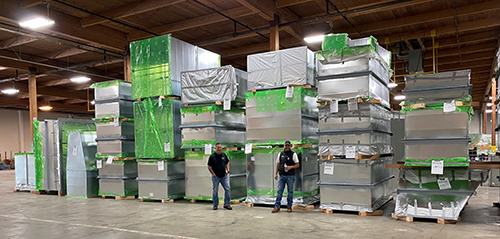
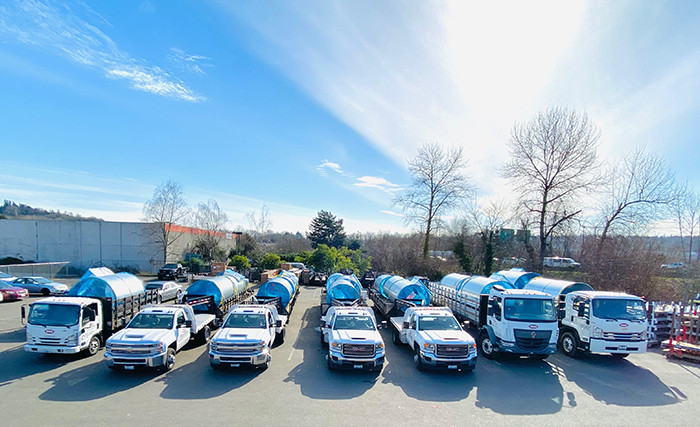
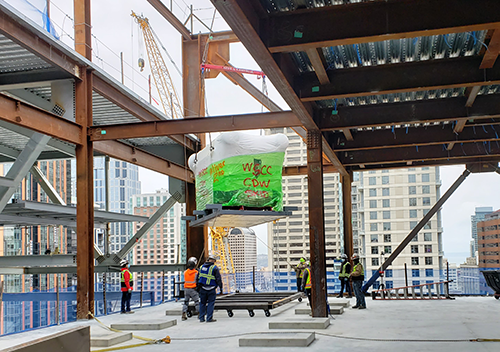

The sheet metal shop and crews from Sheet Metal Workers Local Union 66 fabricated, delivered, and installed more than 1.6 million pounds of ductwork.
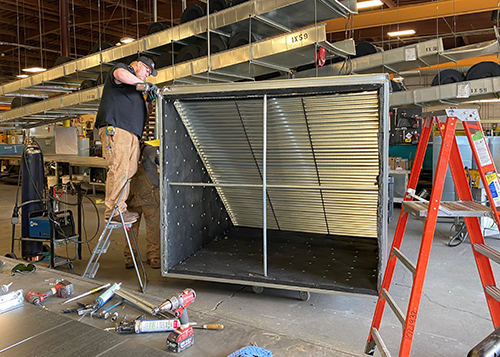
MacDonald-Miller’s pipe-fitting crew from U.A. Plumbers & Steamfitters Local 32 installed, tested, and flushed more than 15 miles of hydronic piping and 100 miles of polyethylene tubing for radiant floors.
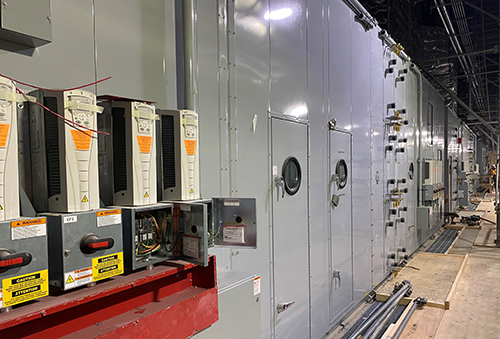
The building automation system was another giant undertaking for this massive building. MacDonald-Miller started this scope of work in 2018 with engineering and completed programing checkout and commissioning in April 2023, making this portion of work a four-and-a-half-year-long project. The building automation system, especially for a building of this size, allows the building engineer to quickly assess the condition of the building. Building engineers can see the hot or cold zones and adjust temperatures with a “click of a button” if there is a problem. The controls system also archives trending data that can be pulled to help troubleshoot equipment or comfort issues. In all, the MacDonald-Miller Honeywell BAS system controls and monitors HVAC, plumbing, mechanical. and electrical systems for the 1.5 million square foot facility serving as the “eyes” and “ears” watching over the HVAC system and will alert the maintenance team when issues arise.
Safety
Most importantly, this work consisted of more than 797,000 hours and was executed safely, with a recordable incident rate of 0.5. To put this into perspective, the national average recordable incident rate in the construction industry is 3.9.
“We did a fantastic job out here on safety,” Hunter said. “It is unheard of. It would be like if four people worked a full 40-year career and only one of them had a recordable incident.”
MacDonald-Miller would not have been as successful on this project without the immense preplanning and collaboration of all team members who were focused and committed to delivering this new space for both the local community in Seattle, as well as the many visitors who will enjoy what the Summit has to offer for years to come.
[Nicole Martin is Brand and Communications Manager at MacDonald-Miller.]