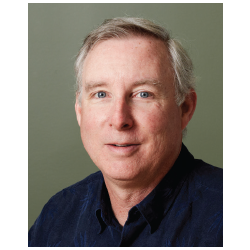
By / Peter Boileau
Chairperson, SMACNA-Western Washington Technical Committee
As we await the incorporation of the 2018 Washington State Energy Code into our design and construction world, postponed from July 1 to November 1 of this year due to the COVID-19 pandemic, we should reflect on our roles as stewards of building energy use and make sure we are thoughtfully balancing high-performance/low energy mechanical systems with providing even better indoor air quality to meet the health and safety needs of the people who will occupy these spaces.
Since 2009, the Washington State Energy Codes have been targeting an ambitious goal to reduce energy use in new residential and commercial buildings from 2006 code levels by 70% by 2031. This has been, and will continue to be, implemented in eight code updates every three years starting in 2009 and ending in 2030. This ambitious goal means an average of a 14% reduction for each code update compared to the previous code’s requirements to meet the 70% target. In past code cycles the focus has been on improving building envelope construction and reducing lighting energy consumption. As these elements of building construction have been optimized, the target has shifted to the next big energy user, fan energy. In the past the use of large fan systems (typically large centralized variable air volume [VAV] systems) has accounted for up to 25% of the total energy used in a building, and, starting with the 2015 energy code, reducing fan energy became the target to meet energy reduction goals.
Current and future codes will prefer the use of dedicated outdoor air systems (DOAS) for providing minimum ventilation and to discourage the use of outside air economizers for ventilation and cooling due to the high energy/fan horsepower requirements for delivering large amounts of outside air into (and out of) buildings. With the use of DOAS systems, heating and cooling are provided by small distributed zone level HVAC equipment, such as water-source heat pumps, variable refrigerant flow (VRF) systems, fan-coil units, sensible-cooling terminal units or chilled beam systems. Again, with an eye to reducing fan horsepower these systems use piped instead of ducted systems to provide heating and cooling to each area of the building. This results in less ductwork required for a building using these systems, and the ductwork provided is typically smaller in size and lower in pressure class, which can impact our business, since we will be fabricating and installing less ductwork on each project as hydronic and refrigerant based piping systems work increases to meet current and future energy code requirements.
But does this shift from high air-change systems to minimum ventilation systems effect indoor air quality? In our quest to reduce our carbon footprint are we stagnating our interior environments? Given the current (and possibly future) concern with pandemics, are we certain that we are truly safe inside buildings that minimize outdoor ventilation rates? Perhaps we should not only think of ourselves and our industry as stewards of energy use in buildings, but also take responsibility and stewardship of the quality of the environments we build for our customers and their occupants. If we are to provide leadership in improved indoor air quality, perhaps we should consider the following ideas:
- Increase outdoor air ventilation rates: new code compliant office building DOAS systems typically provide around 0.15 CFM of outdoor air per square foot of floor area. Enhanced designs to meet LEED ventilation criteria increase this airflow rate to around 0.20 CFM/SF. Not so long ago, a central fan VAV system provided the same building type with between 0.8 and 1.2 CFM per square foot, or four to eight times as much outdoor ventilation when operating in economizer mode. The energy code now discourages economizer operation, which results in reduced and potentially stagnant indoor air, and DOAS systems (equipment and ductwork) that are too small to flush out a building with large amounts of outside air. A better approach might be to increase the DOAS ventilation systems to 0.50 CFM per square foot or more to make sure new buildings are well ventilated and can be flushed rapidly with outside air to improve occupant comfort and safety.
- Better air distribution strategies: Today, most air distribution systems are designed and installed to utilized ceiling supply air diffusers with ceiling return air grilles. These systems rely on large overall airflow rates to mix the air in buildings and induce air movement to evenly mix the air, preventing stratification so floor-to-ceiling temperatures are similar and outdoor air is evenly mixed. However, future energy codes are promoting increased use of hydronic systems to provide temperature control (think chilled beam systems). Ventilation systems are limited in size with this system approach and do not provide the air mixing capabilities that large air systems do. A solution to this might be to consider using vertical laminar air distribution. This type of airflow design is common in large auditorium and theater spaces with overhead supply and floor return (or the opposite) to create vertical airflow instead of horizontal. This approach, and others like ceiling air supply with low-wall returns or raised floor systems move air over the occupants vertically to distribute ventilation evenly and help prevent the spread of viral illnesses. The use of this approach in theaters comes from a long history of understanding that people gathering from different places and sitting in close proximity to each other for performances can be both comfortable and safe, encouraging them to return for another performance in the future. Why not use this idea more often to ensure the buildings we design and build will be equally comfortable and safer from transmission of airborne disease?
- Better air filtration: We typically install air filtration devices depending on the anticipated use of the facility, with office and retail spaces typically getting low-level filtration (typical MERV rating 4-12) and labs and hospitals getting higher levels (MERV rating 13 and higher). Given the current concerns with airborne disease transmission, we should consider installing systems that can use higher levels of filtration than we currently plan for. Better filtration makes for a better indoor environment, and we owe it to our building owner partners to present the option to install a cleaner air system and therefore a better space. In addition to disposable filters, perhaps we should consider other technologies to reduce airborne contaminants like UV systems or even electrostatic precipitators, which can remove more airborne pollutants than HEPA filters can. And in addition to HVAC equipment and duct system filters, perhaps building owners should consider using technologies like combination UV disinfection/lighting systems in high-density locations, such as main building entrances and elevators, to continuously sanitize these high traffic areas to help prevent the spread of harmful diseases.
In these unique times it is incumbent on our industry to create new solutions to keep our indoor environment safe and the people that live and work in the buildings we build healthy and productive. Although energy conservation is one of our critical responsibilities to help reduce our carbon footprint, we also need to prioritize public health in our projects. As long as people choose to live and work indoors in a temperature-controlled environment, as stewards of the indoor environment our industry needs to be cognizant of all aspects of design and construction necessary to create healthy, comfortable, and energy energy efficient spaces. ▪