By / Peter Boileau Chairman of SMACNA-WW ICC Code/Technical Advisory Committee
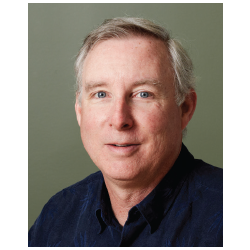
In a previous article, I presented some significant 2018 International Mechanical Code (IMC) changes regarding commercial kitchen ventilation systems, including for the first time code language relating to requirements for “pollution control units” installed in Type 1 grease exhaust systems. In this article, I will present 2018 IMC changes specific to parking garages, residential ventilation and exhaust systems, insulation within plenums, and phenolic duct requirements. The SMACNA-Western Washington Code and Technical Committee has done a recent review and scrub of this new code language, and I would like to share our findings with our fellow SMACNA-WW members.
Section 404.1 – Mechanical Ventilation of Enclosed Parking Garages
The code will be modified to eliminate intermittent operation of garage ventilations systems, which will now be required to operate continuously. The new descriptions states “Mechanical ventilation systems for enclosed parking garages shall operate continuously or shall be automatically operated by means of carbon monoxide detectors applied in conjunction with nitrogen dioxide detectors. Such detectors shall be listed in accordance with UL 2017 and installed in accordance with their listing and the manufacturers’ instructions. Automatic operations shall cycle the ventilation system between the following two modes of operation:
1. Full-on at an airflow rate of not less than 0.75 cfm per square foot of the floor area served.
2. Standby at an airflow rate of not less than 0.05 cfm per square foot of floor area served.
In addition to the above language changes, code section 404.2 has been eliminated as it would be redundant.
The committee was in full agreement that they prefer this approach, as it eliminates time-of-day and occupancy-based strategies that were previously used to start and stop these systems, some of which did not properly ventilate garage spaces in the committee members opinion. This approach also simplifies ductwork systems, as with continuous operation there is no need to install either control or backdraft dampers if certain areas of a garage are running when others are shut-off.
Section 403.3.2.5, Dwelling Unit Ventilation Equipment
A new requirement is added to this section requiring all residential ventilation equipment to be manufactured in accordance with ANSI/AMCA 210-ANSI/ASHRAE 51 requirements and carry a label certifying that it meets these requirements.
The committee clarified that the ANSI/AMCA 210 standard and the ANSI/ASHRAE 51 standard are identical and were developed as a team effort by both organizations. The different nomenclature used is to match each organization’s standards numbering systems. The committee believes that although it is a good idea to require certified fan performance for this equipment, the code section does not address system effects on the fans. The committee has experience with poor installation practices (undersized ducts, excessive offsets/ fittings, etc.) creating systems that significantly reduce the performance of these residential fan systems, and that some language should be added to the code addressing acceptable system design and installation practices as well as the equipment-only performance requirements in order to ensure that the complete system will operate to meet code.
Section 504 – Dryer Exhaust Ducts
Section 504.4 has been modified to require that all clothes dryer ducts be sealed in accordance with Section 603.9. This was not clear in previous codes (only by inference to some language in Section 504, which describes duct construction requirements for these systems). The specific modification states “Clothes dryer exhaust ducts shall be sealed in accordance with Section 603.9”.
Section 504.4.1 now includes added language to clarify requirements for dryer duct exterior termination outlets, including requiring a minimum size of not less than 12.5 square inches for these fittings. The specific added language states, “The passageway of dryer exhaust duct terminals shall be undiminished in size and shall provide an open area of not less than 12.5 square inches”.
Section 504.8.2 has been modified to require that with regard to dryer ducts installed in framing cavities, the cavity depth will allow the installation of the duct without deforming it or forcing it to fit in the available space. This is to ensure that the duct and fittings fit as manufactured and are not deformed, altered, or compressed, which may reduce the overall area of the duct installed. The specific modification states, “Where dryer ducts are enclosed in wall or ceiling cavities, such cavities shall allow the installation of the duct without deformation”.
The committee was in full agreement with these changes, as they provide clear direction to all parties on the proper way to install these systems.
Section 602.2.1.8 – Pipe and Duct Insulation within Plenums
New code language has been added to this section to define what is an acceptable standard for insulation materials used on ductwork and piping located in return air plenums in buildings. The specific code language states, “Pipe and duct insulation contained within plenums, including insulation adhesives, shall have a flame spread index of not more than 25 and a smoke developed index of not more than 50 when tested in accordance with ASTM E84 or UL 723, using the specimen preparation and mounting procedures of ASTM E2231. Pipe and duct insulation shall not flame, glow, smolder, or smoke when tested in accordance with ASTM C411 at the temperature to which they are exposed in service. The test temperature shall not fall below 250 degrees F. Pipe and duct insulation shall be listed and labeled”.
After lengthy and lively discussion among the committee members, the consensus opinion is that the above code change still allows the use of standard fiberglass or foam insulation over metal piping/ductwork in return air plenums to meet code, but it eliminates the use of standard fiberglass/ foam insulation over plastic piping/duct materials installed in return air plenums. If plastic materials are installed (e.g. ABS or PVC piping) these materials must be wrapped with a UL listed fire-rated blanket or wrap to be legally installed in a return air plenum. In addition, it should be noted that the committee was unclear as to whether duct board systems or even acoustical fiberglass wrapping materials meet this new code requirement for flame spread and smoke development in accordance with ASTM E84 or UL 723.
Section 603.5.2 – Phenolic Ducts
This is a new section added to the 2018 code, to describe this newer type of non-metallic duct material. The code language as written states the following:
“Nonmetallic phenolic ducts shall be constructed and installed in accordance with the SMACNA Phenolic Duct Construction Standards.”
For the first time the code now references the SMACNA standard for phenolic duct construction. Phenolic ducts are made of a closed cell rigid foam membrane. Such ducts are self-insulated because the phenolic foamboard has insulating properties, and the duct material can comply with UL 181 as a Class 1 duct. Class 1 ducts have a flame spread index not exceeding 50 when tested to ASTM E84 or UL 723 standards.
The current and previous IMC Section 603.5 addresses nonmetallic ducts, and since phenolic ducts fall into this category, the new section and associated language as stated in the 2018 IMC is appropriate in the opinion of the SMACNA- WW Technical and Code Committee members.
As this new material enters the market, it now has the support of both SMACNA duct construction standards and the IMC code, and its use should be considered by all member contractors as a viable option for future projects. ▪