Pre-construction walkthroughs and changes in virtual reality are now possible at MacDonald-Miller Facility Solutions

As a design-build mechanical contractor with projects throughout the Pacific Northwest, MacDonald-Miller is in the business of designing, installing, and optimizing a building’s HVAC systems. As the construction industry grows, with it the company understands the growing need for technology to bridge gaps between resources, manpower, and time.
The MLAB is a computer-aided virtual environment in the heart of Mac-Miller’s Seattle headquarters. This 750-square-foot room, with 24-foot-tall movie-theater screens for walls, is a space for groups to gather in a multi-use experience of a project. This capability allows any piece of equipment to be modified through software, solving problems before the walls of a building even go up, and saving time and money down the road.
“When people are experiencing their project at the MLAB, there is more than just excitement to walk through their building,” said Luke Barendse, sheet metal detailer for MacMiller. “The value for our customers comes from a sense of control over their project, the ability to make changes to design on the fly, and coordinate in real-time with their teams.”
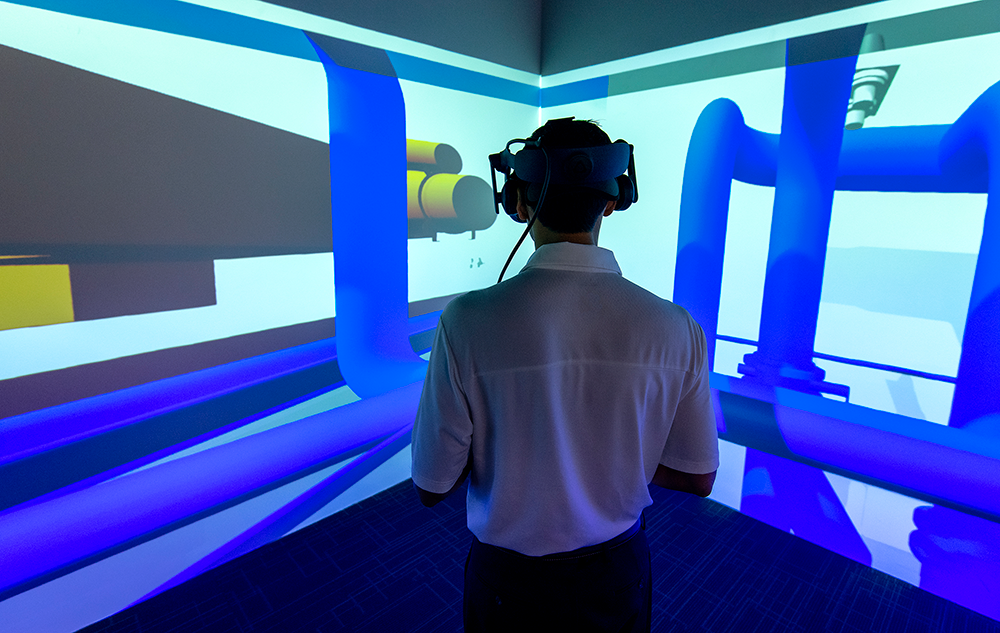
Because of the MLAB, Mac-Miller can take a project, plug in the schedule, and see its aesthetic and functional form and its level of completion at any given date or time. With this level of technology in the industry, the full range of possibilities is yet to be discovered.
As well, this project collaboration does not require everyone to physically be in the MLAB room. Someone in the company’s Tri-Cities office can throw on a virtual reality (VR) headset and join the virtual experience with other members of the team. “This means we can expand our partnerships and streamline our communication with no geographical limitations,” says Bradd Busick, chief information officer.
Mac-Miller’s use of VR technology takes it beyond its the 3D modeling and building information modeling (BIM) it had employed for several years. The expansion will further integrate 4D time simulations and 5D cost analysis, which means labor and time costs are also taken into consideration. For example, using VR the operator can move a piece of equipment and receive instant, real-time feedback on the cost and time associated with the change.
“There are new jobs being created that we haven’t even thought about yet. Perhaps a virtual designer or a virtual engineer. We think this will be a huge market sector.”
“To be able to come in before construction begins, see the structure, and make changes if necessary saves tons of time and money and change orders,” said Nicole Martin, marketing manager at MacDonald-Miller. “The MLAB helps build this collaborative environment for the architect, the owner, the general contractors, and us. I really think it’s going to change the construction industry, and I’m excited for how it’s going to change the workforce. As younger people come to the industry, we’re facing a huge shortage of union workers and field people, so having this technology that they can get excited about is really going to help.”
Virtual reality technology includes the ability to adjust the user settings, including literal perspective. That means even if the VR headset user is 5 foot 9 inches, he can see the project from the perspective of someone who is 5 foot 4 inches.
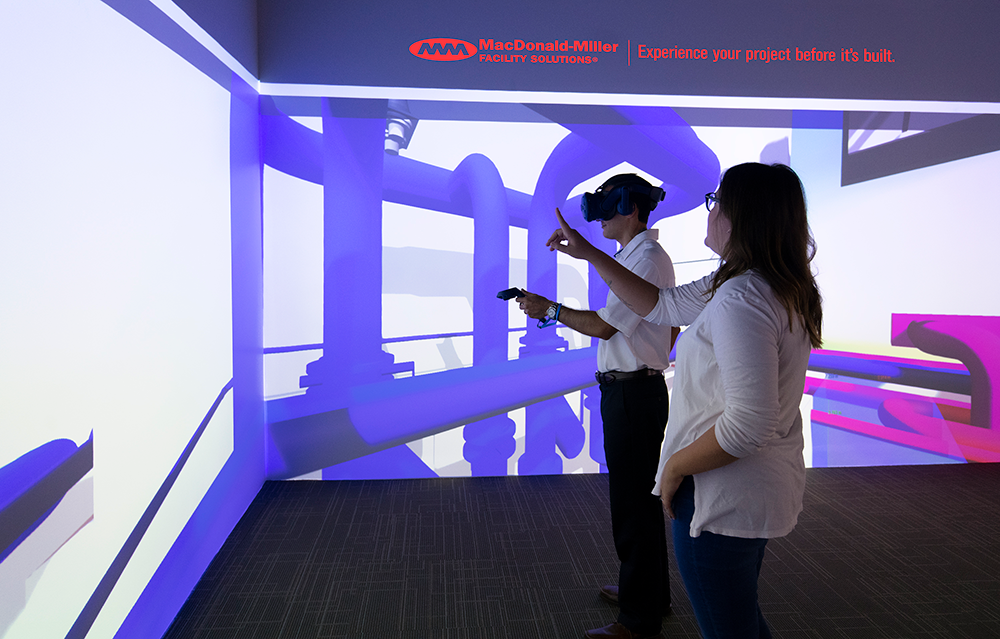
“That is a key factor when you have a facility guy who is 6 foot eight inches come in and you need to know if he will be able to fit into a space comfortably to work,” said Busick.
The introduction of technology streamlines the work process and mitigates the possibility of error, but a strong human workforce is still at the core of these projects’ success.
“At the end of the day, there are still people swinging hammers,” said Bradd Busick, chief information officer at MacDonald-Miller. “But upstream of that, there are new jobs that are being created that we haven’t even thought about yet. Perhaps a virtual designer or a virtual engineer. We think this will be a huge market sector.”
Detailing is another field that will prove vital to the future of the construction industry, especially as 4D and 5D technologies become more prevalent.
“The amount of time saved, material saved, and overall planning saved by designing and coordinating prior to construction is worth it’s weight in gold,” said Barendse. “Being part of the MLAB has been one of the most satisfying and exciting parts of my job. Being able to view a project I’m working on and walk around in it in a literal sense is exciting. The MLAB brings to life projects in a new and fresh way.”
Confident VR will become standard in the future, Mac-Miller is breaking ground with the technology now, and its team is excited to see where the possibilities can take the company, its customers, and its projects.
“We’re the first of our kind, and we’re using this time to work through all the kinks,” said Busick. “We’re calling it a lab because we’re experimenting—we’re trying things out, breaking things in. And we’ve had some pretty wild success with it thus far.”
By Meg Landies
Photos courtesy of MacDonald Miller
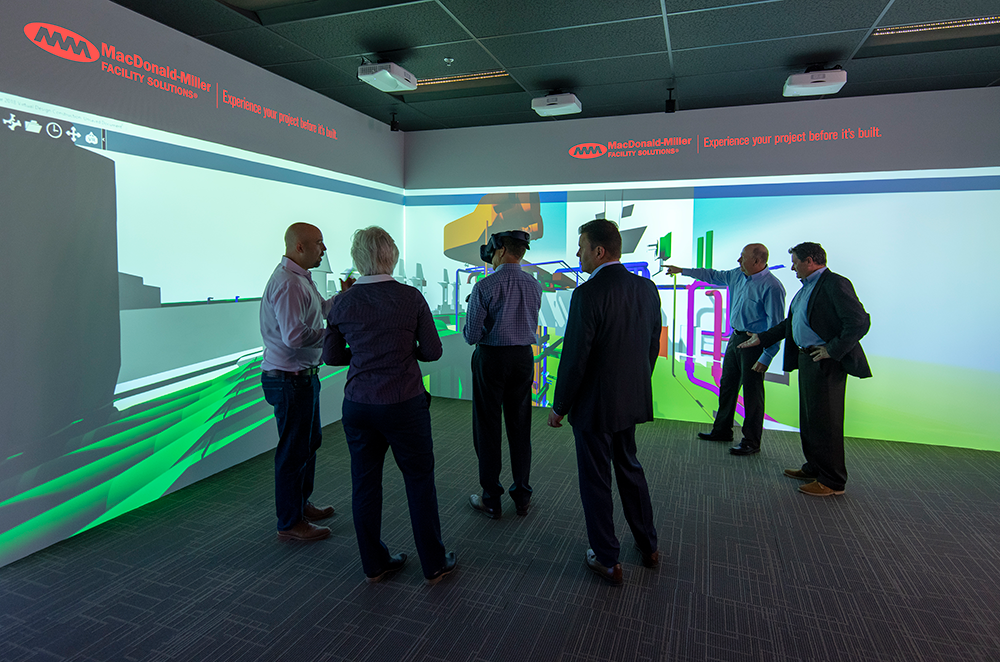