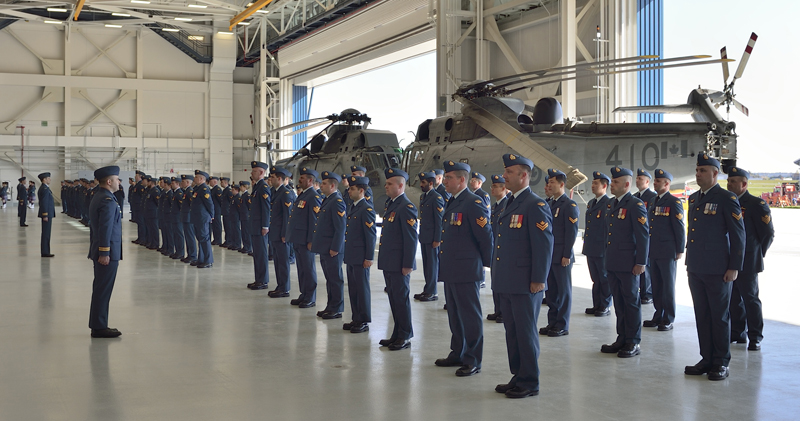

Members of 443 Maritime Helicopter Squadron (443 (MH) Sqn) stand on parade during a ceremony to mark the official opening and naming of their new hanger facility at the Victoria International Airport on April 9, 2015. The ceremony included a parade to celebrate the consecration of colours and name unveiling of the new hanger facility.
Image By: Corporal Malcolm Byers, MARPAC Imaging Services
Department of National Defence, Canada
Willingdon Road, North Saanich
215,000 square feet
Sheet Metal Contractor: Apollo Sheet Metal; foreman – Bill Lutz
Apollo Sheet Metal recently completed work on the $155 million 443 Maritime Helicopter Squadron in North Saanich for Canada’s Department of National Defence (DND)—a four-year build measuring 215,000 square feet upon completion.
The project included a new building, construction of an aircraft apron, a taxiway, an aircraft wash area and refuelling cabinet, a vehicle parking area, a guard house with security barriers, and fencing.
The 443 Squadron operations and maintenance hangar will provide storage for five aircraft, two maintenance bays, an interior wash and maintenance bay, and maintenance shops. Besides administrative and personnel support facilities, the facility will provide warehousing, shop, and work space for the in-service support contractor, while exterior provisions include ramp areas, taxiway, rinse bay, and a refueling area, plus access to roadways, parking lots, and service
Coquitlam-based Apollo Sheet Metal provided all the HVAC ducting, hoods, and HEPA filtration units for the project, as well as AHUs, MUAs, air showers, a paint booth, exhaust arms, and two dust collectors.
Foreman Bill Lutz and his crew installed 1,300 lineal feet of 60″Ø spiral pipe and 750 lineal feet of 48″Ø spiral alone.
“In total, 14,000 lineal feet of spiral was installed totalling almost 90,000 lbs throughout the hangar and administration building,” said Jeremy Hallman, project manager for Apollo Sheet Metal. “We shipped one of our spiral machines to the Island so we could minimize our shipping costs. With so much of the spiral being one size it didn’t allow us to nest it efficiently inside itself for trucking.”
The helicopter hangars presented unique challenges for Apollo’s crew, including steel cross bracing approximately 3 m down from the underside of the roof. “The scissor lifts and ductwork needed to thread through this cross bracing to get to its final location approximately 18m in the air,” said Hallman. “The building is also a post disaster facility which involved more stringent seismic requirements.”
The Island bid deposit rules differ from those on the Lower Mainland, which meant Apollo supplied a lot of equipment that wouldn’t normally fall into its scope. “DND’s attention to detail ensured this was a very good learning experience for me, personally, and provided skills I can carry on to other projects,” said Hallman. “We are currently working on two work packages at CFB Esquimalt.”
Labour for the project was provided by Local 276 on Vancouver Island. “It’s always a challenge hiring a crew of people you are not familiar with,” said Hallman. “Normally we would have our own base crew and hire as required to meet extra demands.
“In this case we send a foreman from the Mainland and he hired the entire crew. We were really pleased with the local talent that came from Local 276.”
The job’s budget and timeline worked out favourably—the pile driving process at the beginning of the project took a little longer than expected, but much of the time was made up over the course of the job.
“It finished a little later than originally scheduled but not by much,” said Hallman. “And the job finished on budget.”